In the modern world, access to safe and clean water is fundamental to public health and overall well-being. In the early 1900’s, Chlorination emerged as a water treatment process that revolutionized how we purify and disinfect water on a large scale. The impact of chlorination on society has been profound, drastically reducing waterborne diseases and saving countless lives. In this blog, we will dive into the science behind chlorination, understanding how this ubiquitous disinfection method works to safeguard our water supply.
The Need for Water Treatment
Before the advent of water treatment, communities were plagued by waterborne illnesses such as cholera, E.coli, typhoid and dysentery. These illnesses could and did spread rapidly, devastating entire populations. To address these public health concerns, two pioneering individuals developed the first water treatment plant to establish the delivery of safe drinking water to homes and businesses.
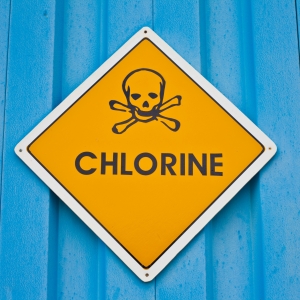
Chlorination is a Game-Changing Discovery
In 1908, a monumental breakthrough occurred when bacteriologist John L. Leal and engineer George W. Fuller introduced the practice of chlorination at the Jersey City Water Supply Company’s Boonton Reservoir in Jersey City, New Jersey, in the first large-scale chlorination of a public drinking water supply in the United States. Initially met with opposition from city officials and the public based on adding “poisonous” chemicals to the drinking water supply, Leal and Fuller persisted, convinced of the potential benefits to the public.
This marked the beginning of an era that would significantly alter the landscape of water purification and serves today as the basis for water treatment purification. By the 1920s, chlorination was a well-established primary means of disinfecting drinking water nationwide.
Today, millions of Americans have access to safe, affordable and abundant drinking water filtered and safely treated with chemical disinfectants due to Leal’s and Fuller’s pioneering engineering triumph.
Mechanism of Chlorination
Chlorination involves the addition of chlorine, either in the form of chlorine gas, sodium hypochlorite (liquid bleach), or calcium hypochlorite (solid granules), to water sources. Upon introduction, the chlorine reacts with various organic and inorganic substances in the water.
Formation of Hypochlorous Acid (HOCl):
Chlorine gas reacts with water (H2O) to form hypochlorous acid (HOCl) and hydrochloric acid (HCl). Hypochlorous acid is the active and most effective form of chlorine for disinfection.
Cl2 + H2O → HOCl + HCl
Disinfection Process:
Hypochlorous acid acts as a powerful disinfectant, attacking and destroying harmful microorganisms by penetrating their cell walls and interfering with enzymatic processes essential for survival. This disrupts the microorganisms’ ability to reproduce and spread, effectively neutralizing the threat of waterborne pathogens.
Chlorine Residual:
Maintaining a chlorine residual in the treated water is crucial to ensure continuous disinfection throughout the distribution system. A chlorine residual refers to the small amount of chlorine that remains in the water after the initial treatment. This residual concentration is a protective barrier against potential contamination during water distribution.
Challenges and Concerns
While chlorination has been a transformative and life-saving water treatment technique, some challenges and concerns are associated with its use.
Disinfection Byproducts (DBPs)
The reaction of chlorine with organic matter in water can lead to the formation of disinfection byproducts (DBPs), such as trihalomethanes (THMs) and haloacetic acids (HAAs). Some DBPs have been linked to potential health risks, including an increased risk of cancer. To address this, water treatment facilities have implemented strategies to minimize DBP formation.
Chlorine Resistance
In recent years, certain microorganisms have shown varying degrees of resistance to chlorine, making it necessary to explore alternative disinfection methods or combine chlorination with other treatment processes.
Conclusion
The science behind chlorination has revolutionized public health by providing access to safe and clean water on a large scale. The disinfection power of chlorine has proven pivotal in reducing waterborne diseases and preventing epidemics. Although challenges persist, ongoing research and advancements in water treatment technology will continue to refine the chlorination process, ensuring that future generations enjoy the benefits of safe and potable water.
Visit rk-water.com for more information.
As the air turns crisp and leaves take on autumn hues, the construction industry must adapt to new challenges and hazards with the changing seasons. While the beauty of fall is undeniable, it’s crucial to remain vigilant about safety on the job site. This blog will dive into essential autumn safety and wellness tips tailored specifically for the construction industry.
Slip and Fall Prevention: A Slippery Slope
Slip and fall accidents are a significant concern in the construction industry, especially during autumn. Studies have shown that wet leaves and frost can significantly increase the risk of falls.
Clear Walkways
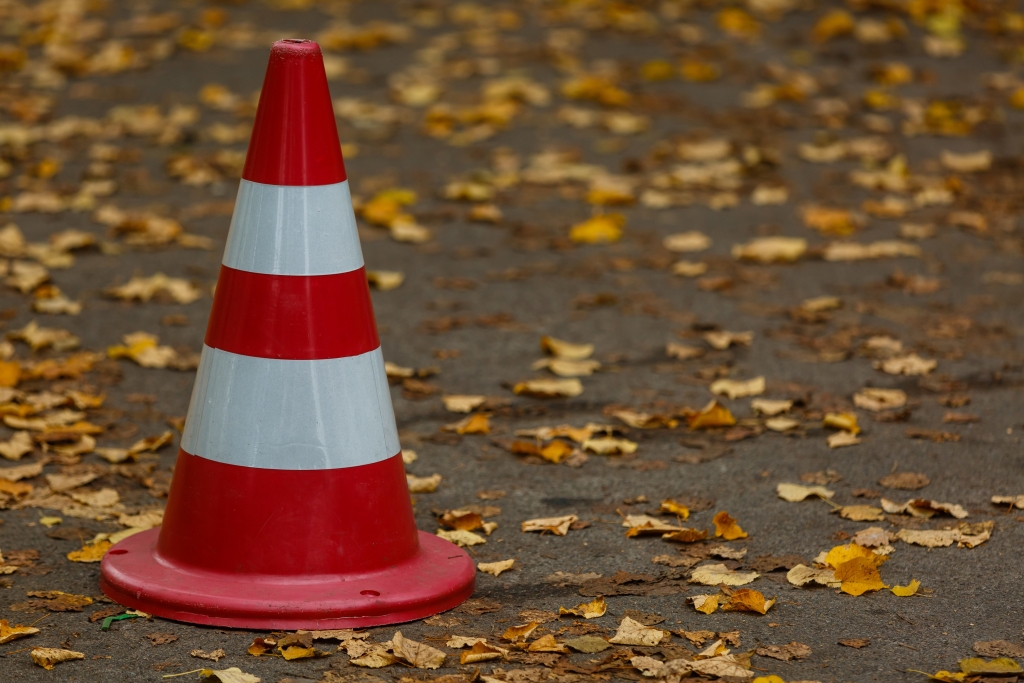
Wet leaves can create slippery conditions. Make it a point to clear walkways, scaffolds and work areas of wet or decaying leaves. Here’s a guide on how to do it effectively.
Frost Alert
Morning frost can make surfaces like roofs, scaffolds, and ladders particularly slippery. Extra caution is advised during the early hours. Learn more about frost hazards.
Footwear
Opt for boots with slip-resistant soles to minimize the risk of falls. Check out safety standards for recommended footwear.
Dress for the Weather: Layering Up
Flexible Layers
Dress in layers that can be easily added or removed as the temperature changes throughout the day. Here are some layering tips.
Task-Appropriate
Ensure you dress for the occasion and are comfortable while carrying out your tasks. Keep yourself warm and cozy with appropriate clothing that suits your needs.
Lighting the Way: Shorter Days, Dimmer Lights
Well-Lit Areas
Ensure that work areas are adequately lit, especially if you’re working during dawn or dusk. Choosing the right lighting can be a daunting task. However, you can make the process much easier with a few helpful tips.
High-Visibility Clothing
When working in areas with low light or near traffic, it is essential to prioritize safety. To ensure visibility and protection, it is crucial to wear high-visibility clothing.
Equipment Maintenance: Pre-Winter Checks
Damage Inspection
Check tools and equipment for any signs of wear and tear that may have occurred during the warmer months. Here’s a maintenance checklist.
Winterization
Prepare machinery for colder temperatures to ensure they operate efficiently throughout the season. Learn how to winterize your machinery.
Training: Seasonal Hazards and Emergency Procedures
Seasonal Hazards
It’s crucial to equip workers with the necessary skills to recognize and manage the potential hazards of autumn, such as slippery surfaces and strong winds. Proper training can ensure a safe and productive work environment for everyone involved.
Emergency Procedures
Anticipate unforeseen weather conditions, such as early snowfall. Being prepared is key, so consider the steps your team can take to ensure your team and jobsite are ready for any situation.
Mental Health: More Than Just Physical Safety
Supportive Environment
Encouraging a positive work culture and supporting employees can lead to a productive and enjoyable work environment.
Mental Health Resources
Provide resources or avenues for workers to seek help for mental health issues. Here are some recommended resources.
Maintaining Safety and Efficiency
The autumn season presents unique challenges to the construction industry, but we can effectively navigate them with proactive measures and a focus on safety. By taking necessary precautions, construction sites can maintain a safe and productive environment during this beautiful time of year.
Grasping the Gravity of High Suicide Rates in the Construction Sector
Research has shown that the construction industry, which is primarily male-dominated, has one of the highest suicide rates among its workforce. Men have been conditioned by society to suppress their emotions, leading to silent suffering. The industry is well-known for its “tough-guy” persona and emphasis on self-sufficiency, appealing to those with risk-taking tendencies. Nonetheless, this culture can also pose obstacles for those seeking mental health support, warranting sensitivity and consideration.
In addition, construction schedules often require extended work hours and job relocations, resulting in feelings of detachment from loved ones. The physical demands of the job, combined with a sense of isolation, can drive individuals to self-medicate with alcohol, drugs, or opioids, further increasing the risk of suicide.
The Significance of Mental Health in the Workplace
Mental health plays a crucial role in construction sites as it directly impacts the safety and well-being of the crew. A mentally healthy workforce is not only happier but also more productive. Key indicators of mental distress include lethargy, lack of motivation, concentration difficulties or absenteeism.
Promoting mental health and wellness within the workplace can foster a positive atmosphere for employees. As a result, this can aid in retaining and recruiting staff members who are interested in pursuing a career in the construction industry.
Comprehending Mental Health
Maintaining good mental health is an ongoing process. Various factors such as personal loss, financial difficulties and relationship issues can negatively impact a person’s mental well-being and ability to concentrate. In environments with a higher risk, operating heavy equipment or getting distracted due to a lack of focus can be dangerous for both workers and the public.
Encouraging an environment where individuals feel comfortable sharing their personal experiences can empower coworkers to check on their crewmates, thereby fostering a safer workspace for everyone involved.
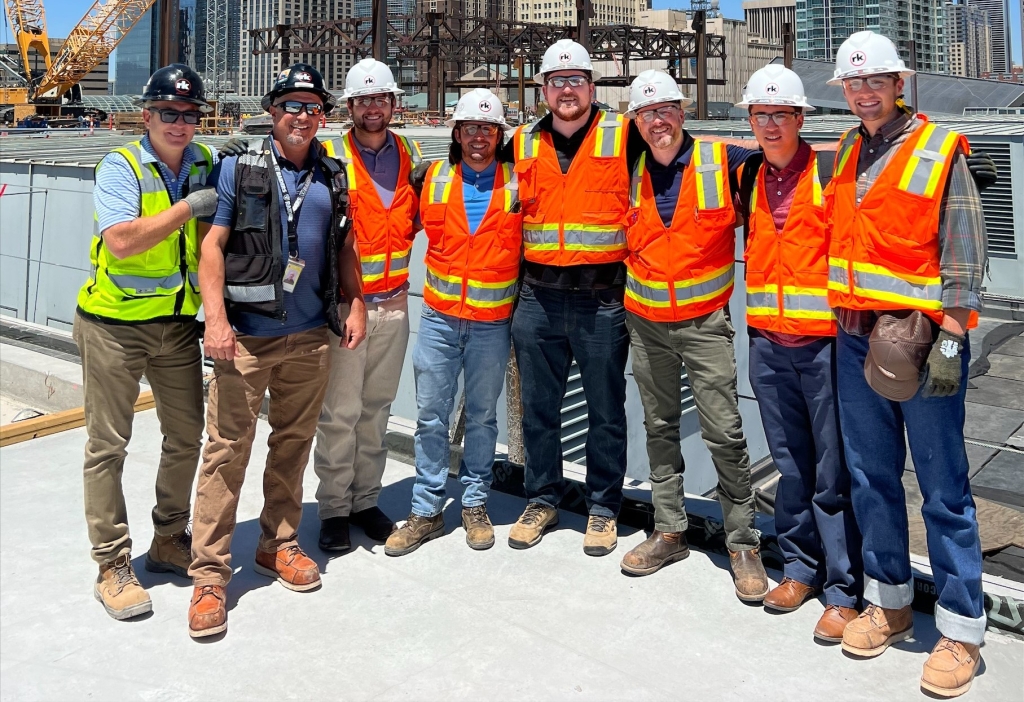
The Role of Management in Driving Change
As a company, it is important to prioritize the well-being of employees. Creating a sense of community and belonging can be achieved by encouraging everyone to be aware of their surroundings and environment. This is especially important in the construction industry, where transitioning from a culture of discipline to one that prioritizes employee mental health and well-being can make a significant impact.
Leaders and employees can provide essential resources to promote mental health by practicing active listening, compassion and empathy towards one another. This approach fosters a supportive environment that enables everyone to thrive.
Identifying Warning Signs on a Jobsite
When observing individuals, paying attention to their behavior and life circumstances can provide valuable insights into their mental and emotional state. Verbal expressions such as discussing suicide, depression, anxiety or feeling like a burden to others can be red flags. Some behaviors, like being absent often, experiencing a sudden decrease in productivity or engaging in risky actions, may suggest that there are underlying problems.
Additionally, personal stressors such as going through a divorce, losing a job or losing a loved one can all impact a person’s emotional well-being. Awareness of these factors can enhance our understanding and enable us to provide better support.
Implementing Measures to Manage and Prevent Workplace Suicide
Companies can play a crucial role in managing and preventing such incidents by taking proactive steps. One of the most important steps is to identify the warning signs, including changes in mood, social withdrawal, talk of wanting to die or giving away personal belongings. Creating a safe environment where employees can openly discuss their issues and feel supported is essential.
Additionally, providing access to mental health resources and safety guides can help employees deal with such issues effectively. Implementing these measures can help companies establish a safe and supportive environment, significantly decreasing the occurrence of suicide in the workplace.
Fostering a Safe Work Environment
Creating a safe and supportive work environment is vital for the well-being of employees. Encouraging open communication about mental health issues, providing access to resources and professional help, and promoting a culture of support can go a long way in achieving this goal. By taking these steps, we can help prevent suicide and save lives in the construction industry.
Prioritizing Employee Mental Health
At RK, the safety and well-being of our employees is of utmost importance. We prioritize creating a work environment that is physically, mentally and emotionally safe for everyone. Safety is our number one core value and priority. We believe in promoting mental health awareness as an integral part of our culture, whether you work on-site, ina shop or in the office. By providing training, our employees are encouraged to check in with their colleagues to express care for their well-being.
Resources for Mental Health and Suicide Prevention
During difficult times, it’s common to feel isolated and helpless. However, it’s important to recognize that seeking help is a courageous act that demonstrates strength rather than weakness. If you or someone you know is struggling with mental health issues or having suicidal thoughts, remember that assistance is readily available.
Crisis Text Line: Text “Hello” to 741741
National Suicide Prevention Hotline: 988 OR 1.800.273.8255 (English), 1.888.628.9454 (Espanol), 1.800.273.8255 (Deaf and Hard of Hearing)
For more information about mental health and suicide prevention in the construction industry, visit:
- The Construction Industry Alliance for Suicide Prevention
- Construction Financial Management Association
- Construction Working Minds
- Man Therapy
Please note that this blog is for informational purposes only. It should not be used as a substitute for professional medical advice, diagnosis or treatment. Always seek the advice of your healthcare provider with any questions you may have regarding a medical condition or mental health symptom. Never disregard professional medical advice or delay in seeking it because of something you have read on this website.
At RK Water, we specialize in providing custom water treatment systems to meet the unique needs of our clients. We take care of every part of the fabrication process, from identifying treatment needs to delivering a fully functional operational water treatment system.
Identifying Water Treatment Needs, Goals and Approach
Every custom water treatment project begins with a thorough assessment of site-specific treatment requirements. By understanding our client’s needs, we design comprehensive water treatment solutions that align with desired outcomes. This includes considering contaminant levels, flow rates, and water quality standards. Our team will engineer a system that meets or exceeds desired standards to meet environmental regulations. Based on the needs and treatment goals, RK Water will explore the best available technologies, such as reverse osmosis, medias, resins and chemical treatment.
Creating Schematic Design and CAD Fabrication Drawing
With the treatment approach determined, our experienced engineers create a schematic design that serves as a blueprint, outlining the treatment system’s layout, equipment arrangement and process flow. Using cutting-edge CAD software, RK Water generates detailed drawings of the fabrication process. These drawings provide precise specifications for each component, including dimensions, materials, connections and assembly instructions.
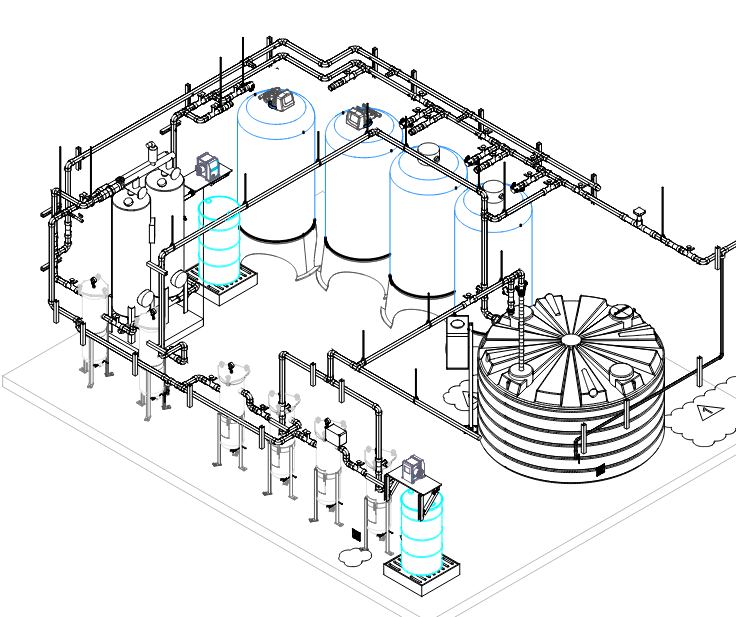
Procurement, Fabrication and Testing
Our in-house team of plumbers and pipefitters will fabricate the designed water treatment systems. By working with other RK business units, we have the in-house capabilities and facilities to ensure every component is installed correctly and according to the design specifications. Once fabrication is complete and signed off, the completed fabricated system is carefully packaged and prepared for shipping to the installation site.
Operational Treatment System
If desired, the RK Waters field team will install the treatment system upon arrival at the site. Before system operation begins, we’ll ensure that all components are properly connected and calibrated, guaranteeing a smooth start-up sequence. Furthermore, RK Water offers ongoing operational and maintenance services, including technical assistance, to keep the treatment system operating at peak performance.
At RK Water, we understand that each water treatment project is unique and requires a tailored approach. Our fabrication process ensures that our clients’ water treatment goals are effectively and efficiently achieved. If you’re looking for a reliable partner in water treatment, count on RK Water to provide comprehensive solutions.
Learn more at rk-water.com.
To better prepare for 2023, business leaders in the construction industry can benefit from knowing the trends that impacted the sector at the end of 2022. Like other sectors in the US economy, the construction industry had to grapple with the increasing inflation and economic downturn that characterized the second half of 2022.
Moreover, business leaders had to cope with industry-specific challenges, such as supply chain disruptions, rising interest rates, and a shortage of skilled workers. Construction companies also needed to keep abreast with emerging construction technologies, such as modular construction and the application of sustainable solutions.
These trends will persist in 2023, but proactive business leaders will leverage them to create competitive advantages.
Inflation, Supply Chain Disruptions, and Interest Rates Continue to Impact the Costs
Inflation
In June 2022, the US inflation rate reached an all-time high of 9.1% since 1981. However, the annual inflation rate slowed from July to a low of 7.1% in November. The slowdown was higher than expert projections, which gives hope for better days ahead. How does the inflation rate impact the construction industry?
Inflation leads to a general increase in the price of commodities across the economy. As an industry, the construction sector suffers direct and indirect impacts of inflation. The immediate effect includes an increase in the price of construction materials, while indirect consequences come from consumers’ decreasing purchasing power. The increase in the cost of construction materials affects the profit of construction companies since they have to pay more to the suppliers. Inflation also affects other construction inputs, such as fuel and electricity. In general, inflation shrinks the profit margins of existing projects as the cost of raw materials and inputs rises.
Interest Rates
Interest rates also went up as we closed out 2022 and the trend persists in 2023. An increase in interest rates impacts the cost of construction materials. Increased interest rates also affect cash flows as borrowing funds becomes expensive. In addition, an increase in interest rates affects demand for construction projects.
Supply Chain Crisis
The Covid-19 pandemic disrupted the global supply chain due to the closure of overseas factories. This disruption led to a crisis in the construction industry caused by a shortage of raw materials.
After economic recoveries in 2021, construction companies rushed to get new suppliers to make up for the delays in deliveries. The rush to get supplies worsened the supply chain crisis in the second half of 2022 as it increased port congestion. This trend continues in 2023, meaning the shortage and cost of construction materials will likely remain high.
Construction companies can overcome the challenges of high inflation, fluctuating interest rates, and supply chain disruptions by investing in innovative and sustainable construction approaches. Innovations that enhance efficiency and increase productivity can help companies reduce production costs and use pricing strategies as their competitive advantage. Investing in supply chain visibility solutions can also help construction companies deal with the supply chain crisis.
Labor Shortage Continues to Be an Issue
Despite the challenges caused by rising inflation, interest rates, and the supply chain crisis, the construction industry remains optimistic. Business leaders can still leverage the trends to create a competitive advantage in the coming decade.
The slowdown in the inflation rate will likely stabilize the economy leading to an expansion of the construction industry or at least a resumption to historic levels. However, even as construction companies remain optimistic about growth in 2023, the labor shortage continues to be an issue.
Although job openings in the construction industry declined to 371,000 in October from an all-time high of 440,000 slots in April 2022, the vacancies are still high. If the trend persists in 2023, construction companies will continue struggling with a skilled labor shortage.
Lead Times and Construction Project Timelines Issues
Labor shortage and supply chain crisis continued to affect the construction industry in the second half of 2022. Long material lead times caused by the global supply chain crisis make it difficult for contractors to complete projects on time.
Shortage of labor makes it even more difficult for contractors to stick to project timelines, which impacts customer satisfaction. Since the trend continues in 2023, contractors must develop innovative ways of reducing lead time challenges. The strategies can include attracting and retaining talented workers and enhancing supply chain visibility.
Finding and Keeping the Right Talent
Attracting and retaining top talent in the industry was a challenge in the second half of 2022. Although labor shortage in the construction industry is not new, the aging workforce and the great resignation have exacerbated the situation. More skilled workers leave the industry, with fewer younger workers ready to replace them.
Human resource managers must develop strategies to attract skilled workers. Construction companies can attract the best talents by paying better wages and improving working conditions. They can also partner with educational institutions to encourage younger workers to join the industry.
Emerging Technologies
The construction industry adopted more new construction technologies in the second half of 2022. This trend will continue in the coming years, with more companies applying technologies like modular construction to reduce costs, meet project timelines, and reduce environmental impacts.
A Higher Focus On Sustainability
Like other sectors, the construction industry is moving towards more sustainable construction solutions. Contractors are using recyclable construction materials and technologies that reduce environmental impacts. Project owners want to hire contractors who can incorporate eco-friendly construction strategies that minimize energy consumption and waste production.
Want to Learn More about Construction Trends?
Understanding the trends in the construction industry gives you insights into the second half of 2023 and the coming years. RK Industries can help you prepare, including giving you tips on attracting and retaining skilled workers in your construction company. Contact us today to learn more.
Construction workers remain an essential element in the industry. Despite mechanization and technological development, the construction industry still depends on workers to complete various projects. However, construction companies are struggling to fill vacancies in their projects. This shortage of construction workers has numerous implications for the industry. The shortage reduces productivity, impacts quality controls, increases the risk of injuries on construction sites, and exerts pressure on construction companies as claims for compensations increase.
Understanding the impacts of labor shortage in the industry can help construction companies develop mitigation measures.
Why Is There a Shortage of Construction Workers?
Several factors contribute to the current shortage of workers in the construction industry. Some factors are within the control of employers in the industry, while others are outside their control. Construction companies should address factors within their control to reduce the impact of labor shortages in the industry. Here are some of the factors leading to the shortage of construction workers.
An aging workforce. The construction industry has been dominated by baby boomers who are currently in their retirement age. Unfortunately, there are few millennials and generation z who are willing to replace the aging workforce. The younger population displays less interest in construction jobs due to working conditions or desire to work in other industries. A disconnect between education institutions and the job market is also working against the construction industry.
The Great Resignation. One of the impacts of the Covid-19 pandemic was great resignation. The containment measures gave workers time to reevaluate their priorities and most workers are now demanding a work-life balance. Demand for jobs that offered better work-life balance increased, while on-site jobs face massive resignations. Most workers approaching their retirement age in the construction industry also left their positions before time.
Challenges in recalling workers laid off during the great recession. The construction industry laid off a considerable percentage of its workforce during the great recession between 2007 and 2008. As the economy improved and construction projects increased after the pandemic, employers are finding it hard to trace the laid-off professionals.
Better wages in other sectors. A significant number of workers who worked in the construction industry before the pandemic have moved to other sectors. Transport and logistics sectors, for instance, employed a considerable number of construction workers.
Which Areas of Construction Are Being the Most Impacted by Construction Labor Shortage?
While almost every area of the construction industry is facing a shortage of workers, the following positions are the hardest to fill.
- Plumbers
- Operations manager
- Project manager
- Electrician
Positions that require unskilled workers are still easy to fill. However, the unskilled workforce can only work with trained workers. The availability of an unskilled workforce can, therefore, not address the labor shortage in the industry.
What Is the Impact of the Lack of Construction Workers?
The shortage in the construction workforce impacts the industry in numerous ways. Like in every other sector, a shortage of skilled personnel leads to productivity, costs, and safety concerns. Contractors unable to fill various positions face the following challenges.
Demand for Construction Services Causing Increased Project Costs
Construction has become more expensive due to labor shortages and supply chain issues. The few skilled workers available for construction jobs demand higher remunerations as the demand for labor increases. Competition for the few workers in the industry requires employers to use monetary incentives to attract talented workers. In addition to a labor shortage, supply chain issues also impact project costs. Contractors have to grapple with the increasing cost of materials before the global supply chain recovers from the impacts of the pandemic.
Projects Are Delayed or Take Much More Time Than Expected
Construction workers are the backbone of any construction project. While technology and mechanization have reduced the number of workers and time required to complete a project, skilled workers are needed to operate the machines. Without enough workers, construction companies delay some projects or prolong the completion time for existing projects. Operations managers working with a limited number of workers have to set their priorities right to keep their companies competitive. However, without the required number of workers, they are forced to put some projects on hold as they wait for workers to fill different vacancies.
Workers Are Feeling Burnout
As the shortage of workers continues to hurt the construction industry, existing workers are forced to work for longer hours to meet project completion deadlines. In an industry that demands the use of physical energy, working for long hours can lead to burnout. Burnout impacts the workers’ physical and mental health leading to reduced productivity. Contractors should be on the lookout for common causes of burnout and empower their employees to overcome them. While burnout can be sudden, there are warning signs for employers to look out for. One of the most common signs of burnout is increased use of alcohol or drugs. Helping the workers deal with burnout increases their productivity and as well as reduces workers’ risk on the construction site.
Quality Control Issues
The labor shortage in the industry means contractors have fewer experienced workers to complete the increasing number of construction projects. Some construction companies may try to proceed with projects without the entire crew. In such cases, unskilled workers are assigned duties that should only be left to professionals.
Increased Builder Risk
The labor shortage in the construction industry is also leading to increased builder risks. The rush to complete projects and poor quality controls caused by labor shortage can lead to dangerous working conditions. Exposing workers struggling with burnout or deploying inadequate/inexperienced workers increases the risk of accidents at the site. Leaving out essential members of the construction crew due to labor shortage also increases the risk of accidents. As contractors deal with the shortage of construction workers, they should organize frequent pieces of training on construction safety.
Want to Attract Talent to Your Construction Company? We Can Help
The shortage of construction workers may impact the operations of your company. However, employing the right recruitment and retention strategies can help you attract qualified workers and retain them in your company. RK can help you position your company as the preferred employer in the construction industry. Contact us to learn more.
Spring is a great time to consider your facility’s cooling tower system. As the weather warms up, many comfort cooling systems shut down in the late fall and winter will soon be put back into operation. Following a few “good housekeeping” procedures are important before these systems are filled with water and started up. These steps allow facilities managers to save money and avoid headaches during the cooling season.
Step 1: Clean Cooling Tower Fill, Basin and Hot Deck
To prepare a cooling system for the upcoming season, clean the cooling tower fill, basin and hot deck. Dirt and debris from the previous cooling season and winter months can build up and must be removed. Failure to remove this debris can foul and plug system components, leading to poor cooling system performance.
Additionally, debris can be a food source for microbiological growth, which can cause corrosion and fouling of heat exchange surfaces and can lead to airborne pathogens such as Legionella. To avoid these issues, debris should be removed from the hot deck and distribution holes. Any broken sprayers or distributors should be repaired or replaced, and the system should be sanitized before being returned to service.
Step 2: Clean and Calibrate Cooling Water Controller
To ensure the optimal functioning of your cooling systems, it’s crucial to clean and calibrate various components. These include the cooling water conductivity controller, probes, flow switch, level controls and chemical metering pumps. Conductivity, pH, and ORP probes that have not been serviced for several months should be cleaned and calibrated. Chemical metering pumps may also need to be cleaned and primed with fresh chemicals before calibration.
Components not properly maintained during the previous season may need to be repaired or replaced to help your cooling systems run smoothly and efficiently. Check that all parts function correctly to keep the cooling water’s chemical balance and prevent scale buildup and corrosion.
Step 3: Clean and Lubricate Fans and Motors
The final step in preparing for the cooling season is cleaning fan housings, lubricating fans and motors, and checking for oil leaks. Ensure fan belts are tight and in working order and replace them if necessary. Oil leaks in fan motors can foul the cooling water system, reducing heat transfer efficiency and causing microbiological growth.
RK Water can assist with your facility needs by providing maintenance services for cooling tower systems, including cleaning and disinfecting the water tanks, checking and repairing leaks, and ensuring that the system is functioning correctly before the start of the cooling season. RK Water’s expertise can help you save money on energy costs and avoid costly repairs down the line.
The construction industry has long been plagued by productivity challenges, hindering its ability to keep pace with other sectors. However, with the adoption of modular construction, the industry is undergoing a transformative shift that is revolutionizing the way buildings are designed and constructed. By leveraging the efficiencies and speed-to-market advantages of modular construction, construction companies and project owners can drastically reduce building time while still delivering high-quality, sustainable buildings. As the demand for commercial construction continues to rise, modular construction represents a game-changing solution that can help meet this demand while simultaneously driving efficiency, productivity, and profitability in the industry.
What is Modular Construction?
Modular construction, also known as off-site construction, is a building method that allows the construction of a building to take place off-site. The structures are constructed under controlled factory conditions and then transported to the construction site. Although the building is done in modules and parts are built in a factory, the building design, construction materials, and standards stick to the blueprint. Since the design and material specification remains the same, one would ask what drives the shift from conventional building methods to modular construction. Here are some of the reasons that explain why the technology has revolutionized the construction industry.
Off-site Construction Saves Time
Modular technology simplifies construction by reducing project completion time. When used effectively, modular construction can reduce construction time by almost 50%. Several factors help reduce the time required to complete a construction project.
First, factory prefabrication and site preparation can happen simultaneously. Delivery of the prefabricated structures and other materials can also be coordinated using just-in-time delivery strategies. Just-in-time deliveries mean materials arrive just when they are needed. This approach enhances efficiency by eliminating downtimes caused by delays in material delivery.
Secondly, off-site construction technology reduces weather delays. Traditionally construction sites have been interrupted by unfavorable weather conditions. Unfavorable weather conditions reduce visibility, which reduces the efficiency of construction workers. In addition, rain or snow may undo previously completed tasks. However, in modular construction, prefabrication happens in a factory setting, which reduces time wasted due to weather delays.
Thirdly, modular construction allows construction mechanization. The prefabricated parts can be moved by heavy-duty equipment that is faster and more efficient than human beings. Construction mechanization allows workers using modular construction technology to complete a building in a single day.
Finally, construction workers do not have to wait for natural processes. At the site, construction workers are only required to assemble the prefabricated parts.
Modular construction is More Cost Effective
Project owners are looking for cost-effective ways of completing their projects. However, even though the project owners explore different ways of cutting costs, they do not want to compromise quality. Modular construction helps the project owners achieve this goal. When compared to conventional methods, off-site construction reduces construction costs in the following ways;
Enhances Efficiency
Modular building technology has revolutionized the construction sector by enhancing efficiency and improving productivity. Since productivity is a function of the overall project cost, boosting it can greatly reduce the total cost of construction. As noted earlier, modular construction reduces downtimes caused by material delays or weather interruptions. Eliminating the downtimes reduces the overall cost of construction.
Improving efficiency benefits both the project owners and construction companies. As project owners enjoy a reduced cost of construction, construction companies can use modular construction technology to improve their pricing strategies.
Reduces Waste
A considerable amount of project cost goes into wasted materials. Reducing material wastage can lower construction costs. Modular construction reduces material waste by up to 80%. Reducing construction waste at the factory and the construction site helps cut the cost of construction.
Reduces Project Time
Reducing project construction time reduces the hours required to complete the project. Since labor is a significant component of the overall project cost, reducing the time required to complete the project makes modular construction a cost-effective building technology.
Modular Construction is a Greener Technology
The construction industry, on pace with other sectors, continues exploring more environmentally-friendly, sustainable production methods. But how is modular construction a sustainable building method?
- The fabrication process is factory-controlled. A factory-controlled production generates less waste compared to on-site construction. Factory managers apply different production methods to enhance efficiency and minimize waste. The prefabricated structures are custom-made, meaning there is minimal on-site waste. The process also reduces on-site pollution.
- Modular construction enhances flexibility and sustainable use of materials. Since the modules are factory constructed and assembled at the site, disassembling is possible. If there is a need for relocation or repurposing of the building, construction workers can disassemble and ship the materials to another site. Reusing construction materials allows the project owners to meet their new needs with minimal energy use and environmental degradation.
Modular Building Technology Meets Building Codes and Standards
Since prefabrication happens in a factory setting, the technology meets or exceeds the building codes and standards. Modular building technology follows product designs and uses specified construction materials to meet regulatory standards.
Improves Safety at the Construction Site
Modular construction happens in a factory setting. With most work being done off-site, modular technology improves safety standards at the construction site. Construction companies that have adopted modular construction reduce downtimes caused by accidents and injuries.
Want to Learn More About Modular Construction? Contact Us Today
Modular construction has transformed the construction industry. The technology not only reduces construction time but makes it cost-efficient and sustainable. RK Industries understands your desire to reduce construction costs and protect the environment. We can help you achieve your objectives by providing more insights into modular construction technology. Contact us today to learn more about construction technologies.
Check for proper licensing first.
When you have a plumbing project that may require excavation work that needs immediate, high-quality service, be sure to check your service provider’s licensing before you hire them to do the job. Proper licensing is crucial whether you are managing the repair and replacement of water, sewer or fire service lines.
Time and time again, RK Service technicians receive calls from property owners who hired a provider to perform work on their property without proper licensing and now need to hire a properly licensed company to complete the job. Though the service provider likely offered to complete the job for a lower price, hiring a company to complete a plumbing project, including excavation work, without proper licensing is extremely risky for the property owner.
Why proper plumbing and excavation licensing is essential.
For example, did you know that fire and water lines are tied to the same mainline? When working on a fire or water line, your service provider must flush and chlorinate the line to properly complete the repair or replacement. If lines are not properly flushed, water lines can become contaminated, affecting the quality and safety of the drinking water for your tenants and potentially other buildings that utilize the same city water line.
These requirements are essential for public health and safety. Unfortunately, many plumbing companies may lack proper licensing or are unaware of license requirements.
What happens if you hire an unlicensed contractor to work on your project?
Though they may offer you a better price for the job, never hire an unlicensed company to do your plumbing work. Here are the top reasons why:
- If the provider is caught operating without the proper licensing, they may lose their rights to obtain the necessary licensure, incur a large fine, and be forced to cease to perform the mitigation work they were hired to complete, ultimately leaving you with a mess and an unfinished project.
- As a property or business owner, you could receive a lien on your property due to hiring a company that does not have proper licensing. At the end of the day, the property owner is responsible for the quality of work. For example, the City of Denver can fine the property owner if the street is not properly completed at the end of the project.
What type of licensing should my service provider have?
Many property owners are unaware the company they hired cannot perform certain services. As a property owner, ensure you understand what types of licensing your service provider needs to complete the work they are hired to perform.
Here is a simple guide to types of licenses that may be used in conjunction with plumbing work. Depending on the project’s location and the type of work to be performed, ensure your provider has the proper license to complete the job.
Types of licenses
- Right-of-Way (ROW) Licenses: Various locations may have different regulations. However, ROW licenses are generally required if performing work in the public right-of-way or on other public property for the jurisdiction licensed in. In addition, there are several sub-categories under ROW, such as Cement Sidewalk Contractor, Sewer Contractor, Excavation Contractor, Paving Contractor, Special Contractor, and Structural Contractor.
- Drainlayer License: This license is required for a Sewer Contractor if the company does not employ a Master Plumber. This license is typically used for drain laying, replacement/repair of sewer lines, storm lines and drainage channels.
- Fire Suppression Systems Contractor – Underground: Underground fire line is the start of any fire protection system as it supplies water to the fire sprinkler systems protecting your facility. A customer may need an excavation service to repair, replace and install an underground fire line.
- Utility Contractor License: A license that incorporates the use of tapping and is performed without shutting down the primary utility line, commonly referred to as a wet tap. The license is used to complete work on a sewer connection or where a building’s sanitary sewer system connects to a city or municipality sewer system. This classification of work is performed by a licensed plumber or utility contractor, and local ordinances must be checked to confirm the correct license.
- Water Service License: This license is used to install or repair service lines and appurtenances from the main up to and including downstream valves. When a water main bursts or breaks and impacts the city water line system, a water service license is required to make repairs.
Research first, then hire.
Hiring a company with proper licensing helps reduce costs in the long run and reduces the time of displacement and discomfort for tenants as the job will be completed the first time properly. Spending more time researching and confirming proper licensing is always worth the effort. To ensure the company hired is licensed and can pull the proper permits for your job, call the city first to verify their licensing status.
If you have a water crisis that requires remediation, repair and installation services, RK Service is fully licensed and ready to work on any job, big or small. For information on RK Service and our emergency 24/7 response time, visit rkservice.com.
As a project engineer in the construction industry, you are responsible for coordinating with various teams to ensure that projects are completed on time and within budget. You may also be involved in designing, planning and implementing various aspects of construction projects.
If you are looking to progress in your career and become a project manager, there are several steps you can take to increase your chances of success.
5 Steps to Become Project Manager
- Gain experience: One of the most important things you can do to progress in your career is gaining as much experience as possible. Working on various projects, taking on additional responsibilities, and seeking opportunities to learn and grow can help achieve this goal.
- Build your skills: As a project manager, you will need to have a wide range of skills, including leadership, communication, problem-solving and decision-making. Focus on developing these skills through on-the-job experience and additional training and education.
- Network: Make an effort to network with other professionals in the field, including project managers, engineers and other key players in the construction industry.
- Earn a relevant degree or certification: While experience and skills are important, many employers look for candidates with a formal education in a related field. Consider earning a degree in construction management or a related field or obtaining a certification, such as a Project Management Professional (PMP) certification.
- Demonstrate your ability to lead: As a project manager, you will lead a team of engineers and other professionals. Show that you can lead by taking on leadership roles within your current organization or volunteer for leadership positions in industry organizations or community groups.
Following these steps can help increase your chances of progressing your career from a project engineer to a project manager. With hard work, dedication, and a focus on building your skills and experience, you can take your career to the next level.
Career Development Opportunities
At RK, we understand the importance of professional development and career progression for our project engineers. That’s why we offer mentorship where experienced project managers can guide and support our engineers’ career growth.
From on-the-job experience to additional training and education opportunities, our project engineers acquire the skills and experience necessary to progress in their careers. We also encourage networking and provide opportunities for our project engineers to connect with other industry professionals and take on leadership roles within our organization.
If you’re a project engineer looking to take the next step in your career, RK is here to support you every step of the way!